Millwall FC's 20,000 capacity ground, the first new all
seater stadium to be completed after the Taylor Report on the
Hillsborough disaster, was designed with with effective crowd management
in mind, the escape routes are short and direct.
The ground incorporates a local-authority sports centre and is well
equipped with restaurants bars and toilet facilities, making it a
flexible, multi use venue. |
Architect's
account NICK PARKINSON
Partner, The
Miller Partnership
The project
outline brief was to provide an economical 20,000-capacity all-seater
football stadium which retained the close and compact (not to say
intimidating) atmosphere of the Den and would be available by the 1993
close-season deadline.
It was to be a
joint venture with the borough of Lewisham, which would provide the land
and some investment. In return, a sports centre for the local community
was to be constructed as part of the development.
The site is
triangular, surrounded on two sides by elevated railway lines, and on
the third by light industrial units. The proportions of the site were
such that the position was virtually predetermined at the south east end
of the site to ensure adequate clearances around its perimeter for
emergency egress and access.
Hemmed in by railway lines and a
power station, the shape of the site dictated the positions of the
stadium and sports hall |
The stadium
consists of four individual stands. The north and south stands are
identical single-concourse stands, the west stand houses the club
accommodation block and main hospitality suites, and the east contains
32 executive boxes. Both west and cast stands have concourses at two
levels.
To maintain
spectator proximity to the pitch, we have kept the lower seating decks
quite shallow (14 seating rows maximum). As a result, the upper tiers
are quite steep and are kept close to the pitch.
With safety of
paramount importance in stadium design, we planned the escape routes
carefully to be as short and direct as possible. All the seating decks
are designed to allow a five-minute maximum escape time.
The concourses
themselves are segmented into 30m maximum lengths and are planned so
that should an incident occur in any one concourse compartment, this can
immediately be shut down without compromising the escape times.
Externally, the
building is dominated by the main circular structural columns and
triangulated tie-bars which support the main cantilever roofs.
The west and east
stands, with their double concourses and hospitality and club
accommodation areas, extend beyond this main column structure line and
are clad simply in profiled-metal and flat-metal cladding panels and
masonry blockwork.
We situated the
sports centre on the north end of the site, where there was sufficient
space to accommodate three floodlit five-a-side pitches, two play areas
and 60 dedicated car-parking spaces.
Construction of
the new stadium started in May 1992, with a deadline for completion of
August 1993. In June 1992, as the pilling rigs were busy on site, the
club signed its three-year contract with Ogden Entertainment Services
(UK). With this appointment, the whole concept changed from football
stadium to multi-use venue.
It became
necessary to incorporate a number of fundamental changes into the design
whole the building works progressed, within a very tight programme.
These included
changes to the stands, which were no longer to he separate buildings but
were to be linked by a continuous ground floor concourse.
The turnstiles
were relocated from the rear of each stand and grouped in banks of nine
in each corner, allowing easy access to the pitch for concerts and other
events, while also allowing access to more than one stand if required,
and easy segregation. We also increased the toilet facilities (the
stadium has the highest toilet-per-capita ratio of any venue in the
country) so that they not only cater for the 6: 11 male:female spectator
ratio inherent in football, but can also be adapted easily for 1: 1
ratio spectator events.
The number of
refreshment bars throughout the concourse was increased and their range
upgraded to make an extensive range of fast foods available before,
during and after each event.
The hospitality
areas were also upgraded. We redesigned the east-stand executive boxes
to incorporate individual wc’s. Holding kitchens and food-preparation
areas were introduced to provide immediate catering services. In the
west stand, the main kitchen was increased in capacity so that it could
serve a 400-seater restaurant.
The hospitality
area itself was redesigned to provide maximum flexibility: movable
screens allow the space to he opened out or segmented as required, with
bars immediately accessible to each area, serving a, diversity of uses
from conferences and exhibitions to receptions and restaurants.
We adjusted the
pitch and spacing of the north and south stands to accommodate different
field events, |
from
football - including under-21 and B internationals - to rugby league,
American football and hockey.
Because of the
restrictions of the site and the need to retain adequate perimeter
circulation, allied to obvious financial restrictions, it was not
possible to extend the building outwards to house this increased
accommodation. Instead, every square metre of available space under the
seating decks was used.
This often led to
elaborate routing of services, particularly ductwork, in order to
maintain usable headroom, and called for dexterity and imagination by
consultants and contractors.
Structural
engineer's account BILL REID
Director,
Thorburn
The problems were
many and varied. With the site enclosed on three sides by railway
embankments, access options were limited and it was necessary to
construct a new retaining wall along the southern site boundary to
create access additional to that available from the existing road
system.
Soil conditions
underlying Senegal Fields are poor, with a thick layer of peat covering
the majority of the area. We considered removing the peat, but rejected
this on cost grounds. We left it in place and adjusted the design to
accommodate its presence.
This means that
all structures are supported on piles, and that drainage, hardstandings
and the playing surface have been arranged in recognition of the fact
that small seasonal movements of the ground surface will occur.
To obviate
potential problems with methane generation within the peat, a venting
system was installed under the ground-floor slabs.
The structures
are supported by 70-tonne working capacity driven cast in-situ concrete
piles founded on the underlying chalk bedrock at an average depth of
19m.
Structural steel
frames support composite concrete floor slabs and precast concrete
seating deck units. The main columns supporting the roof consist of
762mm diameter concrete-filled steel tubes. Lateral stability to resist
both static and dynamic forces comes from steel bracing between the
columns in both the longitudinal and lateral directions.
The roof consists
of steel trusses fabricated from self-weathering steel. We designed
these to give tolerance in erection so that the nose level of the
trusses could be adjusted to the achieve consistency, prior to their
being locked together with lateral trusses at mid span and at the front.
The roof deck is
suspended under the trusses and supported by a structural gutter. We
have used this detail, which allows a plane roof soffit, successfully on
several projects, as it is easy to build and maintain, and prevents
birds roosting under the roof canopy.
The playing
surface consists of a highly permeable 4:1 sand/organic soil mixture.
Drainage is achieved via porous pipes at 3m centres. Under-soil heating
is provided by a piped hot-water system with the 12mm diameter pipes
installed at 300mm centres.
The pitch was
sown during October 1992 and was used for the first time last month.
Fire
engineer's account IAN
SMITH
Director, Fire
Safety Engineering Consultants
Using a
fire-engineering approach has allowed much of the structural steelwork
in the stadium to remain unprotected against fire. Fire-protection
materials have only been used in areas defined as high-risk.
We achieved this
by demonstrating that an unprotected structure would be acceptable in
certain areas provided certain criteria were met.
The Guide to
Safety at Sports Grounds indicates that stands should be constructed in
accordance with the Building Regulations, which list requirements in
functional terms. The relevant Approved Documents relate to those
regulations concerned with stability and compartmentation:
B3(1) The
building shall be designed and constructed so that in the event of fire
its stability will be maintained for a reasonable period
B3(3) To inhibit
the spread of fire within the building, it shall be sub-divided with
fire-resisting construction to an extent appropriate to the size and
intended use of the building.
These
requirements can be met either by following the guidance of Approved
Documents or, as we did, by using another procedure - provided one can
demonstrate that it satisfies the criteria.
(Continued Below) |
Client's account
DAVID MARKS
Group financial
controller, Millwall Holdings
Our decision to
move from the 'Den', home to Millwall Football Club (nicknamed the
Lions) for more than 80 years, was based on two criteria - the need to
adhere to the Taylor report and create an all-seater stadium which, in
terms of size and facilities, would take Millwall into the twenty-first
century, and the non-viability (in terms of both construction and
finance) of adapting the old ground into an all-seater modern stadium.
In choosing the
location of the new ground, we knew that it was essential not to
alienate and uproot loyal fans by moving any great distance from the
original Den. When the current site, only minutes from the old ground,
became available, it was therefore the ideal and obvious choice
for Millwall's new home.
Initially, we were
introduced to Ogden Entertainment Services as potential
caterers/operators of the food and beverage outlet. Once we realised the
extent of Ogdens expertise in stadium-and arena-facilities management -
it currently manages more than 100 facilities in the US alone
- we tapped into its expertise and involved it in most aspects of the
stadium, from design to operation, and in particular in the booking of
non-football events.
We chose the
design team for the project because of its experience in stadium design
and project management. The Miller Partnership, the architect, and
Thorburn, the consulting engineer, have worked on projects that include
Ibrox Park, Murrayfield's east stand and Windsor Park, Belfast.
The brief for the
design did change. Initially, we wanted a 25,000 all-seater stadium with
one main stand that included a hospitality area.
Following
discussions with the design team, we agreed that the club and spectators
would be better served by basing the design on a 20,000 all-seater, with
free access from one stand to the next, giving due regard to customer
flow. It was also vital that there were sufficient services for
customers in terms of toilets, telephones, catering and disabled
facilities.
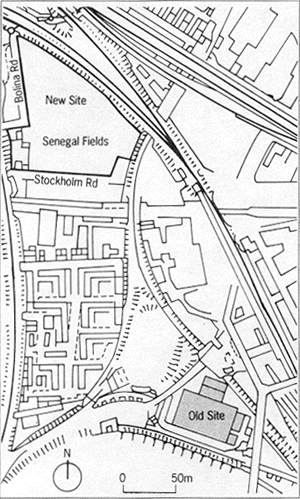
The new ground is within walking
distance of the old one. |
Operator’s
account JON SINIGAGLIA
Stadium director,
Ogden Entertainment Services
Once we become
involved with a project, we feel it is important to be consulted on
design and construction matters such as crowd management, concession
control, circulation and general venue operations. It is our experience
that a lot of other facilities could have worked much better if they had
been laid out differently. from the start.
At Millwall, we
had to ensure that a building primarily used as a football stadium could
also function effectively as a 29,000-capacity venue for concerts.
At the north end,
designated as the stage end, there are 750 three-phase amps. The sports
hall, which has been built as part of the arrangement with Lewisham
Leisure Services, will provide space for equipment, production offices,
crews an d catering. And one of the three hospitality suites can also be
used as an extra changing room.
Although the
stadium does not carry any staging, sound or lighting, we have ensured
that there are the basic facilities to make it very quick and easy for
concert people to load in and out. Each of the four corners of the venue
can allow trucks right into the stadium so we can load right up to the
stage position, and outside there is a facility to use segregated
parking areas for scaffolding. These areas are accessible from any part
of the venue.
For events like
concerts we will have mobile catering and merchandising facilities on
the site. A permanent merchandising shop has been built into the front
of the stadium so that most people will pass it as they approach the
venue. |
|
Fire engineer's
account IAN SMITH
Director, Fire
Safety Engineering Consultants
(Continued from above)
We used the
B55950 Code to define the temperatures likely to initiate structural
failure, and the inherent fire resistance of the members in the BS 426
Part 20121 test.
Data from real
fire experiments, relating fire-load density, ventilation, limiting
temperature and the Hp/A value of the section (where Hp = perimeter
exposed to fire attack [m] and A=cross-sectional area [m2] defined a
critical value of fire load which could initiate failure in a fully
developed fire.
In areas where
the fire-load density was expected to be less than the critical value,
the structure was left unprotected - i.e., the main concourse areas,
toilets and sealed voids.
The remaining
areas, such as refreshment bars, plant rooms, offices, hospitality
areas, and club facilities, were all considered as ‘high-risk’ and
were therefore separated from the adjacent ‘low-risk’ areas by fire
resisting construction. The steel members in the high-risk areas were
protected to satisfy a one-hour standard.
In carrying out the analysis we had to
bear in mind the range of potential uses of the spaces, but nonetheless
we were able to achieve considerable cost savings. Only about 40 per
cent of the steelwork in the four new stands was fire-protected. |
Appraisal by
CALLUM MURRAY
Freelance
journalist
There was a time
when everyone hated Millwall - and Millwall knew it. 'We are Millwall,
we are Millwall, no one likes us, we
don't care!', its supporters sang (and still sing) with relish.
A few seasons
ago, when Millwall was promoted, briefly, to the then First Division
(now Premier League), there was a collective groan from the supporters
of other clubs. No one wanted the louts from south-east London playing
in the division where the beautiful game was supposed to flourish. No
one wanted Millwall's fans rampaging around their stadia, ripping up the
seats and urinating wherever they felt like it.
The club's
reputation as the pit bull of English football was bolstered by its
ancient, low-lying, corrugated metal stadium situated in a derelict
industrial pocket, surrounded by railway arches and scrap yards.
Visiting teams were afraid of playing there - and that was how
Millwall's supporters liked it.
But what the
other First Division teams hadn’t realised was that a revolution was
already under way at Millwall. It began with the club winning a series
of awards for its community and youth schemes and has culminated in the
first all-new, all-seater, major-league stadium to he completed in
England since the publication of the Taylor Report on the Hillsborough
disaster of 1989.
Unusually for a
football club, Millwall found that Lewisham, the local planning
authority, was sympathetic to its aim of moving to a new stadium. |
The borough
provided the site - Senegal Fields, an under used area of playing fields
- and a small grant. In return, the club is providing off street car
parking, a sports centre for use by the community and funding for the
creation of new public open space.
On the evidence
of Millwall first pre-season friendly against Sporting Lisbon, the
stadium scores on sight lines and safety, but not on access. Getting to
and from the seating decks is no problem, but access to the stadium by
car and by public transport remains difficult.
The inaugural
match was mainly attended by Millwall's own fans, most of whom live
locally. But what will happen when Manchester United comes down to play
in a cup match?
As for the
facilities, the stadium coped triumphantly with a near-capacity crowd.
The ultimate test of a football stadium's toilets and refreshment
outlets comes at half-time. At most stadiums you are lucky if you
get to use one of the two. At Millwall, you could easily use both.
Consequently, the
concourses were relatively relaxed places in which to have a beer or a
burger. And the crowd's accumulated urine stayed firmly in the urinals,
where it belonged.
What the stadium
doesn’t offer, by the architect Nick Parkinson's own admission, is any
genuine design innovations - the design is, to use his words, 'tried and
tested' .
Taken singly, any
of its elements could be found on other stadia in the country. What is
unusual is to find them applied so consistently throughout a
stadium. The
result is a building that is robust, efficient and well adapted to its
immediate purpose of staging league football.
And the game?
Millwall lost 2:1 in a bad tempered affair that included a penalty and
much mindless, off-the-ball provocation and retaliation. Amid all the
change, its good to see some of the old traditions being maintained.
Cost comment
TOM HINDLE
Associate
director, Thorburn
The project was
carried out under the fifth edition of the ICE Conditions of Contract,
with Thorburn acting as engineer. The civil-engineering method of
measurement was used for the principal stadium elements, but for the
sports centre and trades work within the stadium the standard method of
measurement (SMM7) for building works was adopted.
There were a
number of abnormal elements involved in the project, principally related
to site-specific features. The presence of surface fill material
overlying a layer of peat up to 1.5m thick required the adoption of
piled foundations, methane protection measures, special bedding and
support system for drainage, suspended ground floors and capping layers. |
Cost analysis of the
New London Stadium: £15.5m Total Cost
|
|